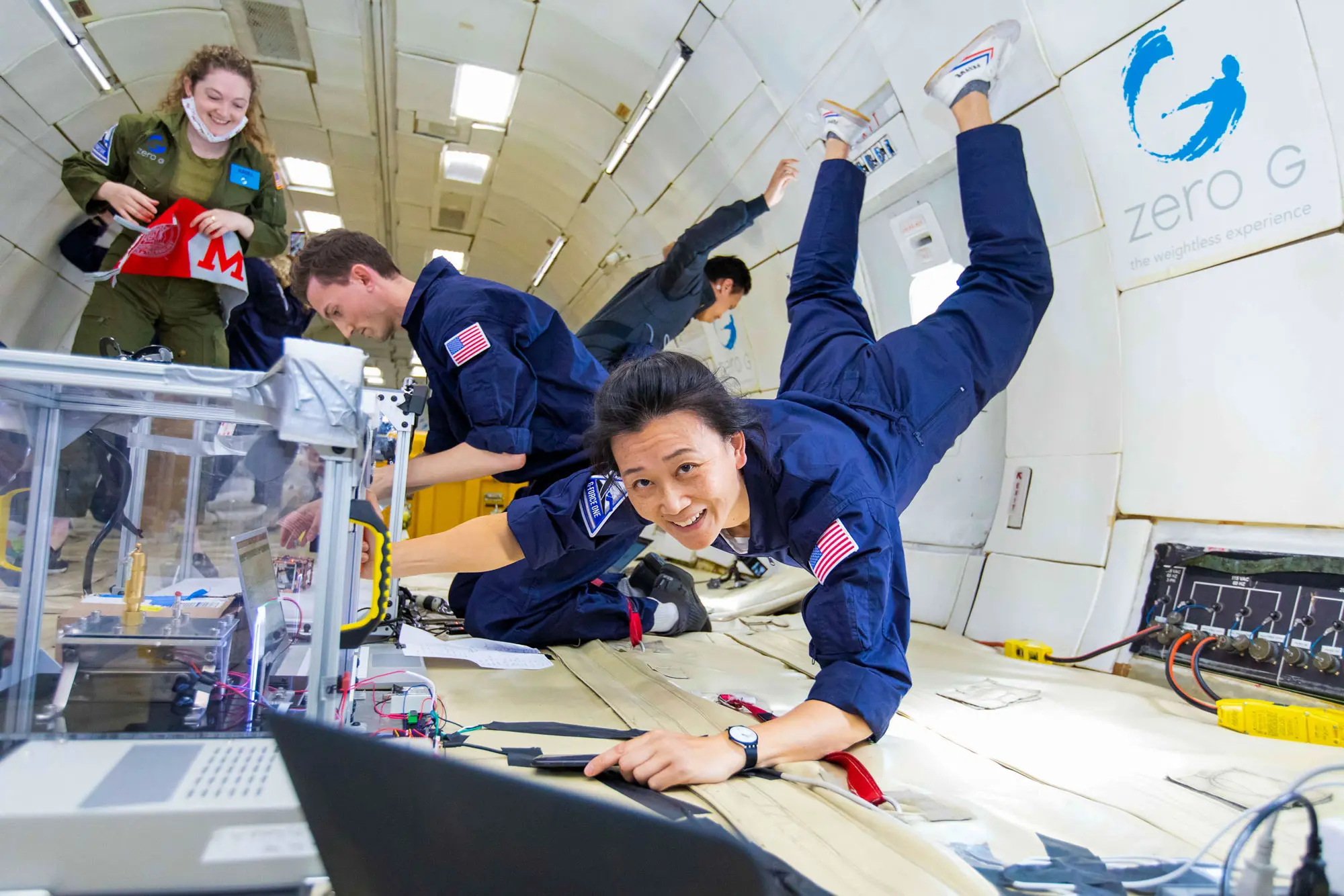
Your Space Tech Testbed
Collect invaluable data for your space-bound technologies.
Minimize Risk
Imagine preparing to deploy your new space technology.
You’ve spent years and millions of dollars researching, prototyping, and hypothesizing. Now it’s time to launch, but there’s only one catch: Your technology has never actually been tested in zero gravity.
Are you confident in your launch without testing?
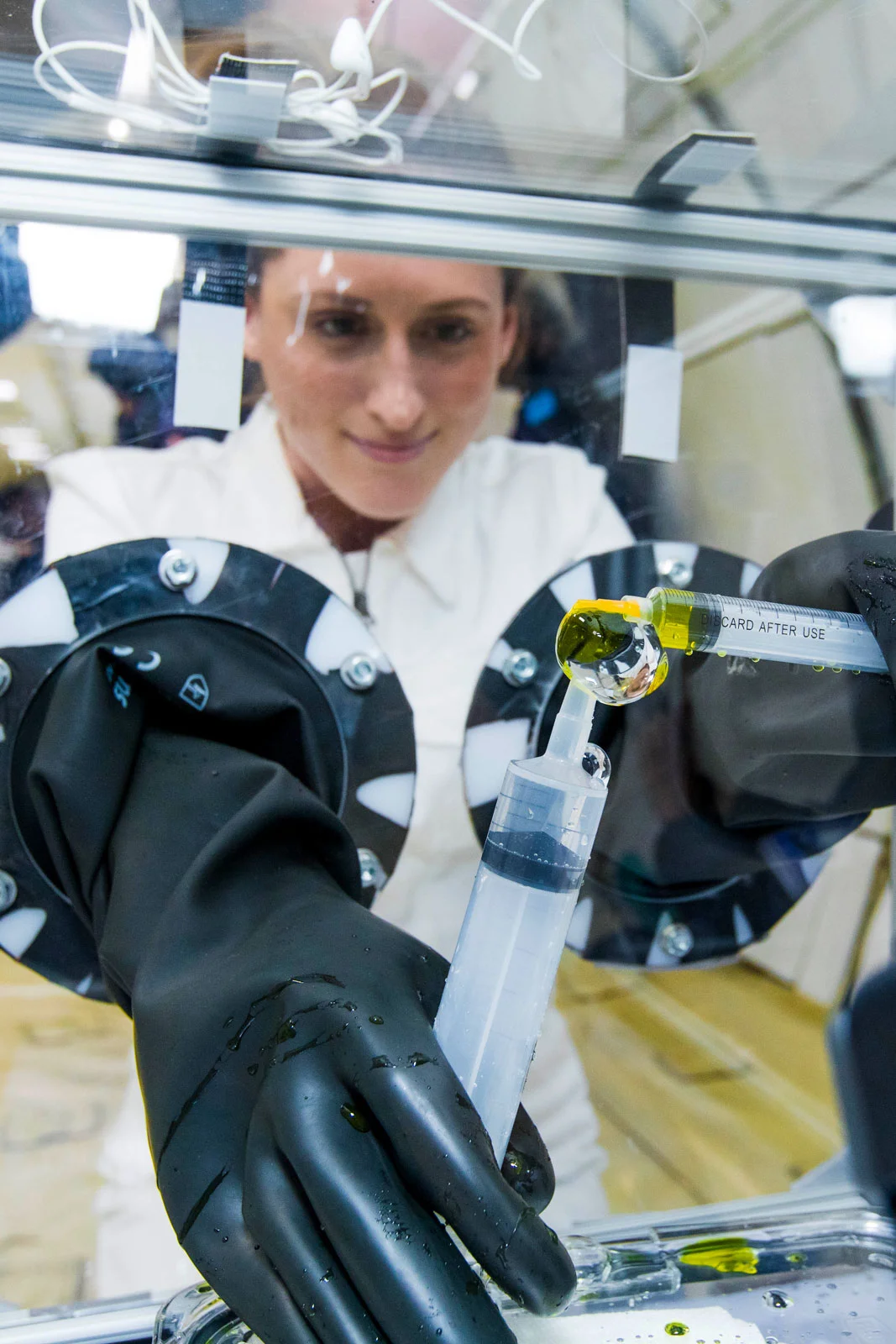
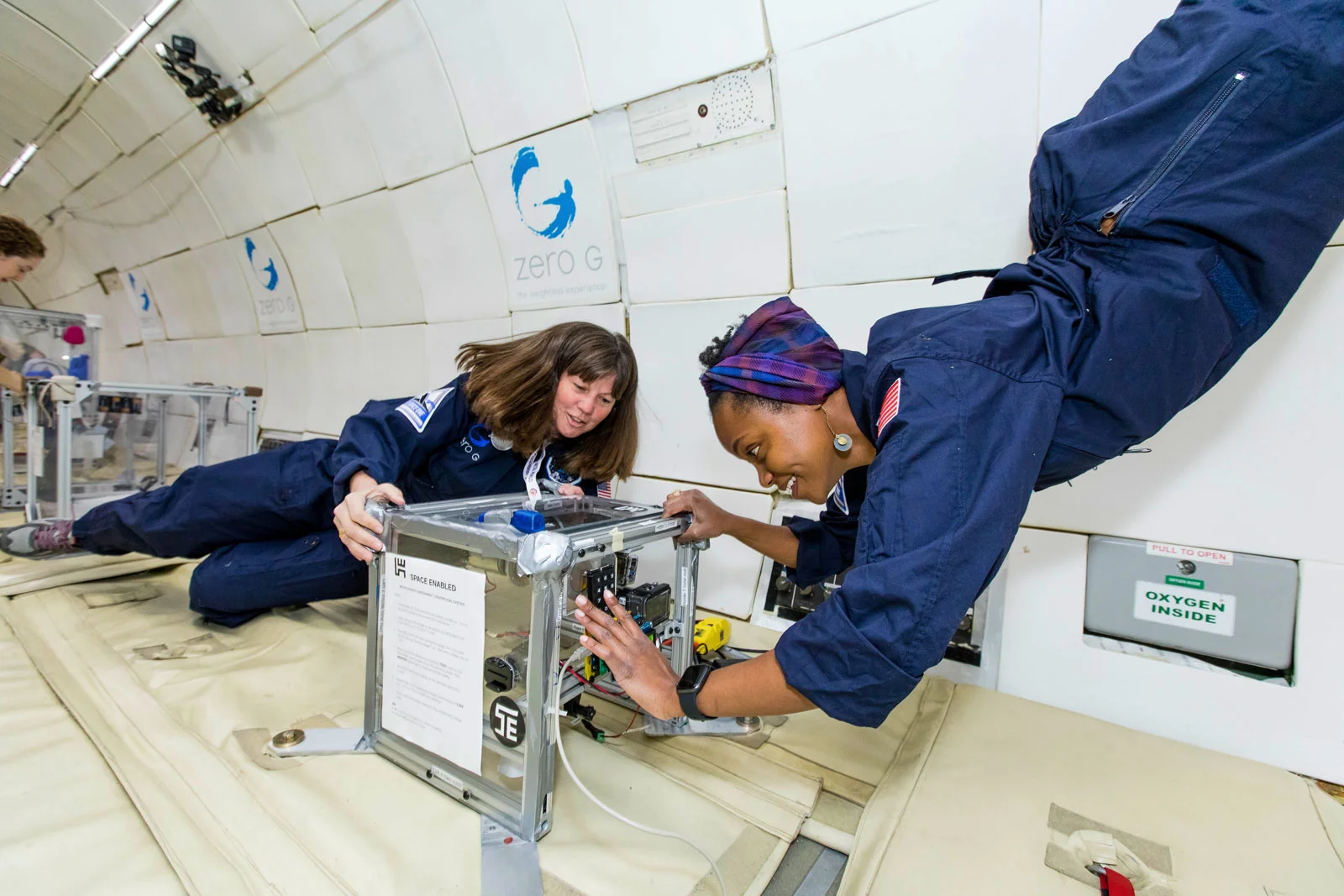
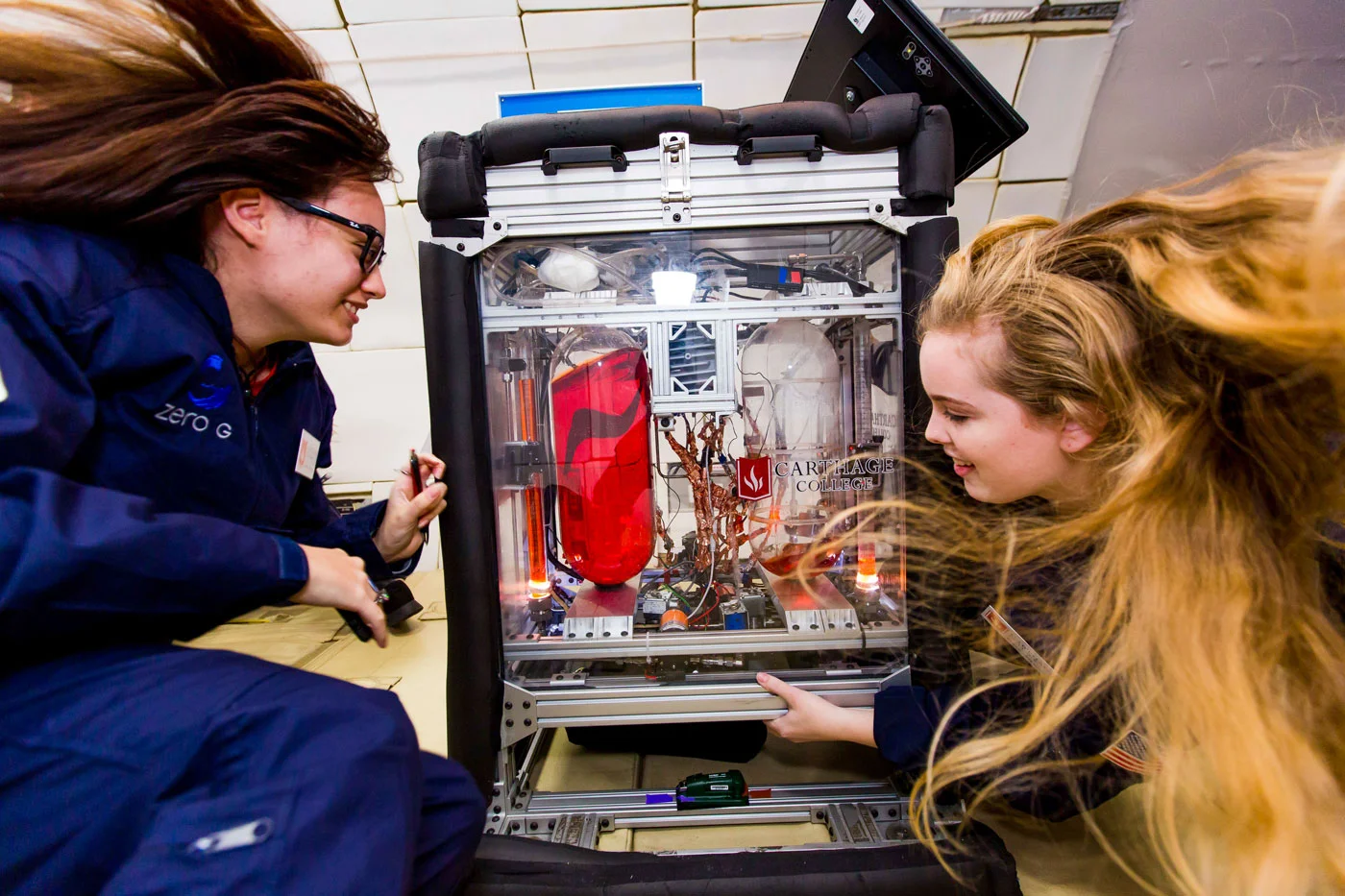
Trusted By The Space Industry Elite
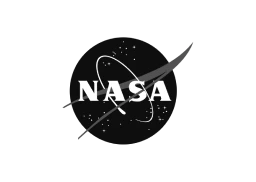
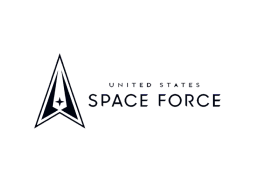

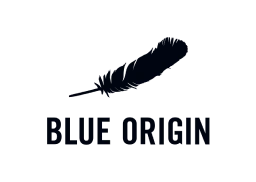
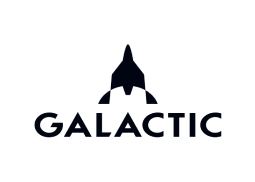
Launch With Confidence
Parabolic flights are a critical first step towards achieving your space research objectives. Our team of experts help you collect the quality data that your research demands, and launch with confidence when the time comes.
Past Research Missions
Collect Quality Cryogenic Data
Test the behavior of fluids and fundamental physics with cryogenic liquids in zero gravity.
Make Medical Discoveries
Shape the future of healthcare by learning about microgravity’s impact on medical technologies, innovations, the human body, and more.
Forge The Future
Use zero gravity flights to investigate how various materials and manufacturing methods perform in space.
Find The Right Formula
Gain a better understanding of chemical adhesion and related behaviors on zero gravity flights.
Solve Real-World Problems
Put a number of materials to the test in true zero gravity to elevate the quality of your findings.
Explore Sustainable Living
Test, document, and re-test to find out more about what it’s like to grow and cook food in space.
A Spotless Safety Record
20
Years In Operation
900+
Flights
2,400+
Research Payloads
17,000+
Parabolas
22,500+
Guests
Pricing
Mixed Payload (Handheld)
$10,300
+ Tax
Book a single seat aboard a shared flight with other researchers. Best for small, unmounted experiments.
*If Booked More Than 90 Days In Advance
Mixed Payload (5' x 10' Section)
$60,200
+ Tax
Book a 5' x 10' section aboard a shared flight with other researchers. Best for small/medium-sized experiments and rapid prototyping.
*If Booked More Than 90 Days In Advance
Mixed Payload (10' x 10' Section)
$70,400
+ Tax
Book a 10' x 10' section aboard a shared flight with other researchers. Best for medium-sized experiments and rapid prototyping.
*If Booked More Than 90 Days In Advance
Private Research Flight
$295,000
+ Tax
Book an entire research charter for exclusive access to the aircraft. Ideal for large-scale experiments, full-team participation, and complex equipment setups.
*If Booked More Than 90 Days In Advance
Take Your First Step Into Space™
Research Flights
The Process
We’ll handle the flight planning. You focus on the science.
Get Started
Choose between a private charter, mixed payload, or handheld experiment, and submit the Test Data Summary form to help us understand your research objectives.
Receive Quote
We will provide you with a cost quote and any additional considerations while preparing your research
Execute Contracts
Confirm your flight by signing a standard research contract and paying the deposit
Process Payload
Submit your Payload Integration package (PIP) so our team can file all required FAA paperwork and approvals on your behalf
Prepare For Takeoff
Complete a Test Readiness Review (TRR) 1 day prior to flight, install your experiment, and get ready to fly.
Frequently Asked Questions...
Getting you ready for your weightless experience.
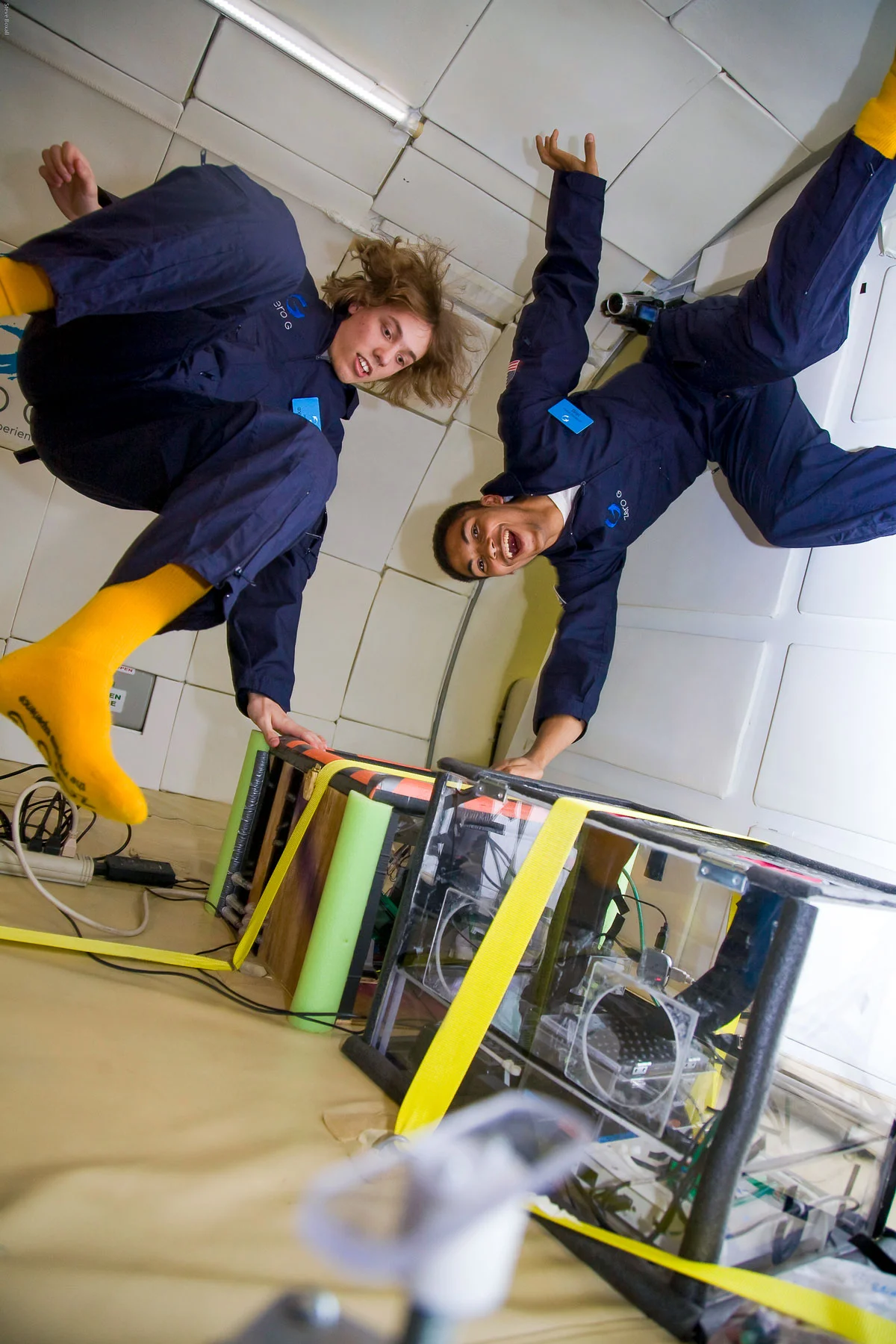
Can I test my technology in Lunar or Martian gravity?
Absolutely! Zero-G can precisely create Martian and Lunar gravity environments inside the aircraft, giving you the perfect opportunity to test your technology before launch.
How do mixed payload flights work?
Twice a year, Zero-G offers mixed payload campaigns where research teams can purchase individual payload slots on a shared flight with other researchers. These flights are ideal for teams that require multiple flights but don’t need the entire aircraft to themselves.
Mixed payload campaigns are typically held in the spring and fall. Payload slots are reserved on a first-come, first-served basis.
How many parabolas are included on a research flight?
Research flights include 30 parabolas—double the number of a public or private flight—giving you up to 15 minutes of microgravity. This extended time allows you to gather as much data as possible for your research.
Have you flown zero gravity research like mine before?
Between quietly supporting the entire space industry for 20 years, and flying over 2,300+ research payloads, it is highly likely that we have supported an experiment similar to yours.
Can I select my own custom flight profile?
Yes, when booking a private research charter, you can customize your flight profile with up to 30 parabolas. Select your preferred mix of Lunar, Martian, and zero gravity parabolas, and our expert pilots will handle the rest.
For mixed payload campaigns, flight profiles are pre-set in advance.
Float Us A Line
A member of our team will contact you shortly.
Oops! Something went wrong while submitting the form.